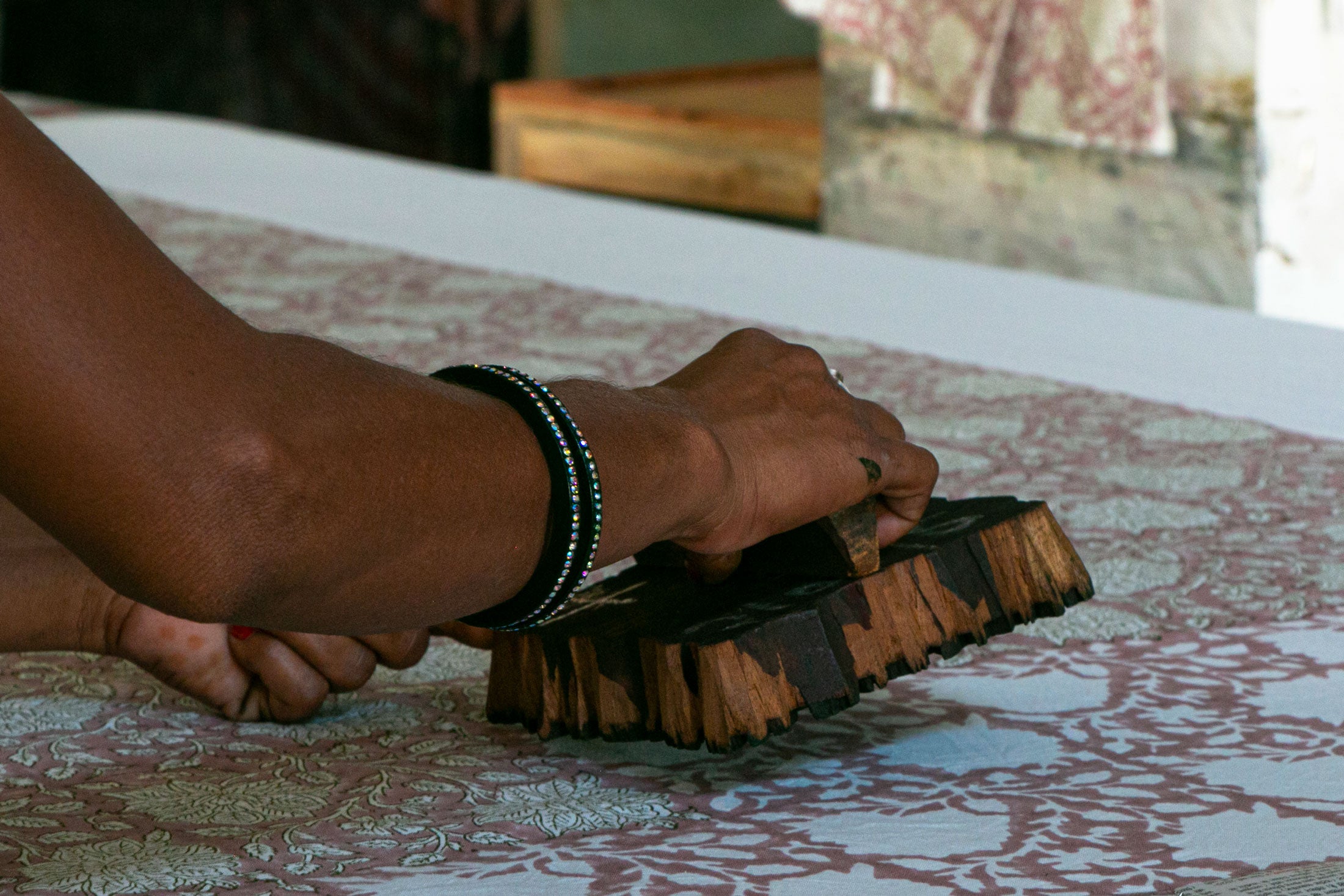
The Story Behind our Table Linen | The Ancient Art of Block Printing
Hand Block Printing
Hand block printing is an ancient textile technique which originated centuries ago in the region of Rajasthan, in India. What seems like a fairly straight forward process, takes incredible skill, practice and a very steady hand!
Here at L&M Home, we have a great appreciation for this artisan process, which is why we continue to bring block printed table linen to the Australian market. We love the idea that each tablecloth tells a story of history and craftsmanship, and any small inconsistencies in the print is what makes each piece unique from the next.
The Wood Block
The wood used to make the block is most commonly teak, which is soaked in oil for up to two weeks to help soften the grain of the timber. A highly trained block maker traces the intricate design onto the wood, then uses a hammer and chisel to carve out the pattern. A handle is also carved out of each block, along with several small holes to help release air and any excess dye.
Carving the block is a highly skilled, labour-intensive process. It can take 2-4 craftsmen several days to complete a single design on a printing block. Multiple blocks are often required for one design, to print various colours and shapes. On average, a set of blocks is used to print on 2000 metres of fabric.
The Dyes
Traditional vegetable and mineral dyes are still used in the block print process today, however some non-toxic chemical dyes have been introduced help withstand washing, and to ensure the prints are colourfast.
Care must still be taken with your tablecloth to ensure the longevity of the colour. Wash in cold or warm water on a gentle cycle, and keep out of the harsh Australian sun to prevent rapid fading.
The Printing
A printer begins by drawing a length of fabric from a large roll over the printing table and fastening it with pins to avoid any wrinkles or movement in the cloth. The fabric is then marked out with chalk and a ruler to show where the first stamp of the block is to be applied.
The printer dips the wooden printing block in a dye tray, then stamps the block on the fabric with a hard pound of the fist, ensuring an even print. This step is repeated from left to right, aligning the blocks perfectly by eye, a skill which comes from years of experience.
The artisan prints the outline pattern first and takes care to ensure it is applied very precisely, as the outline leads the whole design. Several ‘fill’ blocks are then used to layer up the colours and complete the design. A high level of skill is required for the precise placement of the blocks and the right application of pressure. The fabric is then hung out to dry in the hot Rajasthan sun between each application of colour.
Keeping the Tradition Alive
Despite there being faster and cheaper methods of textile manufacturing, block printing has resisted mechanisation throughout the years and is still done entirely by hand. L&M Home will continue to introduce hand block printed textiles into our collections. We love that this traditional craft is kept alive and thriving in today’s modern interiors. Block printing provides a sustainable livelihood to local artisans and their families, and we are proud to support these communities.